射出成型機(英語表記:Injection Molding Machine)とはプラスチックなどの合成樹脂の加工方法の事です。プラスチック射出成形機ともいい、素材を溶かし(溶融)、型に流し込み(射出・成形)、固める(冷却)、取出すといった工程を1台で処理することができる工作機械です。
1.概要
金属とプラスチックの違いはありますが、金属の金型鋳造法と似ています。鋳造は、金属の融点を超える温度で比較的低粘度の液状にて低圧で充填を行う(流し込まれる)のに対して、射出成形は比較的低い温度 (180~450℃)で高圧で成形する違いがあります。
プラスチックの語源は【可塑性(plasticity:プラスチシティ)】です。可塑性(かそせい)とは個体に外力を加えて変形させた時に、その力を取り除いても元に戻らずに成型される性質を意味です。
プラスチック(合成樹脂)のように、外から熱・圧力を加えて成形できる性質を利用した方式です。
金属鋳造でもダイカストは熱融した材料を金型へ圧入する方法は同じです。樹脂射出成型の方が溶融温度は低いですが素材が高温に弱い性質のため温度管理がよりシビアである点が違います。
射出成形に使用される金型で凸部は雄型でコア(Core)とも呼ばれ、凹部は雌型でキャビティー(Cavity)と呼ばれています。射出成形機へ金型を取り付ける場合、必ずキャビティーが固定側となりコアが可動側となります。
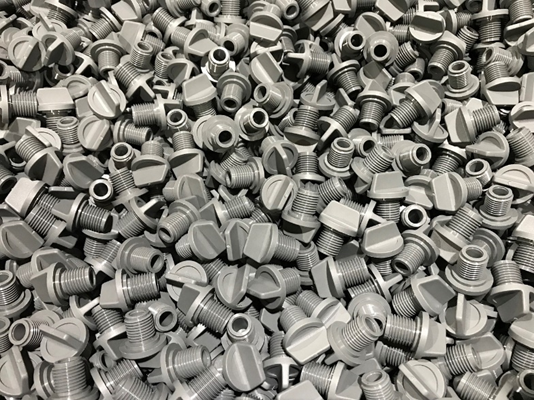
2.射出成型機の構造
射出成型機はその機会の大小に関係なく三つの機構(装置)からできています。
①コントローラ
成形条件等を制御する装置です。
最近はNC化(コンピュータ化)が進み射出成型の各種設定値(速度・圧力・シリンダーの温度・金型の温度・材料の射出量等)など必要な条件をデジタル処理しています。
②射出ユニット
プラスチックの材料を投入するホッパー、材料を加熱するシリンダー、噴射ノズルなどが含まれ、材料を熱で溶かしてスクリュウで押し出して金型に注入するための装置です。
③型締めユニット
金型の装着や金型の開閉を行い、材料の圧力に抵抗して金型を閉じておいたり、材料の突き出しを行う装置です。
3.射出成型機の工程について
①型締め
金型には 固定側(キャビティー)と可動側(コア)があります。この稼働側が固定側に移動して金型が閉まることを型締めといいます。この状態で溶けたプラスチック樹脂を金型内に充填するとき金型には強い圧力が加わりこの時金型の締め付けが弱いと成型した際に製品にバリ等の不具合が発生します。
②ノズル接
金型に溶かしたプラスチック樹脂を注入にするために、シリンダーノズルを金型に密着させる工程のことです。
③射出・保圧
溶けたプラスチック樹脂を速度調整して金型内に注入することを射出といいます。射出後溶けたプラスチックに一定の圧力を加えることを保圧といいます。これは溶けたプレスチックがシリンダーに逆流することを防ぐ事と溶けたプラスチック樹脂が冷えると収縮するために、射出した樹脂に圧力を加えて調整しています。
④冷却
金型の内部にオイルや水等で一定温度に保った金型で射出したプラスチック樹脂を冷却します。この冷却は一般的な冷たい温度ではなく、20℃~100℃の使用している素材に最適な温度です。100℃で冷却というと熱いのではと思われますが、プラスチック樹脂の温度はおおよそ300℃付近ですので100℃でも冷却して固化します。
⑤型開き
冷却された樹脂が固まり成形品が出来上がると、成形品を取り出すために金型を開きます。このことを型開きといい可動側の金型が成型品と一緒に開きます。
⑥突き出し
金型が開いたら、イジェクターピンで成形品を押し出して取出します。そのまま機械の下に落とすこともできますが成形品にキズがついたり、変形する事があり製品品質に影響がでる場合がありますので、通常は取出し機等を使って取出し作業を行います。
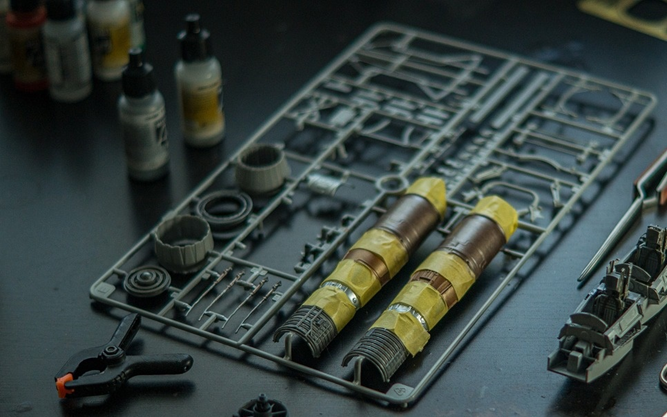
4.射出成形機の種類について
射出成型機の射出工程や型締め工程に必要な動力源として代表的なものとしまして、電動式と油圧式の2つの方式があります。
4-1電動式射出成型機について
電動式はサーボモータ等を用いて、速度・圧力・位置決め等の動作のすべてを制御する方式です。電動式ではトグル式と直圧式の型締めがありますが、トグル式がほとんどです。
〇電動式のメリット
・高精度の製品:
電動式ではサーボモータ等の使用することで射出装置の制御の精度が正確にできるため、成形品の寸法や形状を一定に保つことが容易になり、製品の成形精度が高くなります。これにより油圧式ではできなかった高い精度が必要な製品の製作が可能になります。
・省エネ:
電動式は必要時にモータを駆動させるので、油圧式に比べて使用エネルギーが少なくなりますので省エネになります。
〇電動式のデメリット
サーボモータ等は設定された内容に正確に素早く応答すしますがモータの出力容量以上の出力を出すことができません。
サーボは正確な制度の制御ができる反面設定条件が難しいというデメリットもあり、設定が難しいですが電気式はデジタル処理ですので一度設定が決まれば再現性にはすぐれている反面もあります。(デメリットがメリットになります)
(*)直圧式:
型の中央部を押す構造なので金型の中央部に型締め力が加わりやすく、周囲に力が加わりにくい方式となります。
・直圧式は、真ん中に型締力がかかりやすい。
・直圧式は、中央に比べて周りにバリが発生しやすくなります。
(*)トグル式:
トグルリンク(アーム)といわれる人間の関節の様な動きで稼働盤の周囲に力をかけて動かす方式です。
・トグル式は、トグルリンク部に比べて真ん中にバリが発生しやすい。
・トグル式は、トグルリンクに力が加わりやすく中央部に力が加わりづらいです。中央部に型締め力が加わりづらい欠点に対して、最近の成型機は中央部に型締め圧力が加わるような構造に改良されています。
4-2油圧式射出成型機
油圧式は文字通りに油を閉じ込めて、その圧力を離れた場所に伝えることで大きな力を出す仕組みです。これには物理法則の「パスカルの定理」が応用されており、古くから利用されている動力方式です。油圧式では直圧式の型締めのみ対応しています。
〇油圧式のメリット
・油は圧縮性が少ない特性があるので高圧力の生成が可能です。
・電動式に比べて射出成型機の単価が安価になります。
・構造が単純になりますのでメンテナンスが容易になります。
〇油圧式のデメリット
電動式に比べて
・消費電力が大きい。
・外乱環境の影響を受けやすい。
・電気式に比べて騒音(作動音)が大きい。
・細かな制御が苦手。
・作動油の管理やオイル漏れのリスクがあります。
4-3射出成型機の機種選定の目安
射出成型機を検討する際に必要な項目(仕様)は「型締め力」と「金型サイズ」です。金型を射出成型機にセットして、可塑化したプラスチック素材を金型に注入する際には金型内部には高い圧力がかかります。この時の圧力が稼働側の金型を押して開こうとしますので、締め付ける必要があります。この締め付ける力が弱いと製品にバリが発生したり、製品のサイズが金型より大きなサイズになってしまって仕様通りの精度に製品が出来上がらなくなります。
したがって射出成型機では、金型を締め付ける力を型締め力として規定し、N(ニュートン)やtf(トンフォース)などの力を表す単位で表記します。
(*)最近では力の単位は N(ニュートン)の利用に統一されています。
型締め力の計算は簡単ですが次式になります。
F=p*A/1000
F:必要型締め力(tf)
p:金型内の圧力(kgf/cm2)
A:投影面積の合計(cm2)
(*)Fは(tf)になります。
1(kgf)=9.8(N)ですので(参考まで)
(*)投影面積:
金型の稼働側・固定側両方の金型に圧力がかかっている面積を言います。