プリント基板実装(PCB実装)とは各種電子部品をプリント基板(Printed Circuit Board, PCB)に取り付ける工程や技術など一連の作業全般の事を言います。この作業により電子回路が構築され各デバイスが正しく機能するようになります。基板実装には各種(いくつかの)ことなる手法や技術があり、それぞれの用途などに応じて使い分けます。
1.スルホール実装(Through-Hole Technology:THT)
スルホール実装は電子部品のリード(足)をプリント基板(PCB)に開けられた穴(スルホール)に通して基板の反対側でリード(足)をはんだ付けする実装方法となります。この方法は表面実装(SMT)が主流になる前の昔ながら実装方法ですが、現在でも幅広く用いられています。
(*)スルホール:プリント基板(絶縁物)に部品のリードを通すために穴に銅メッキを施しはんだ付けが可能な状態に仕上げた穴です。
1-1 スルホール実装の特徴
①高い物理的強度:
リードがプリント基板を貫通してはんだ付けされているために機械的な強度は非常に高いものになります。このことによって衝撃や振動が多い環境でも高い信頼性となります。
②信頼性:
スルホール実装は特にパワー系の電力供給や高い信頼性が要求される電子回路で使用されます。リードの接触面が広く接合し安定している為に長寿命製品に適しています。
③電気的特性:
電気的な接続がしっかりとしているので電気的なインピーダンスや接触抵抗が低くなる傾向があるのでパワーエレクトロ二クスや大電流を扱う回路に向いています。
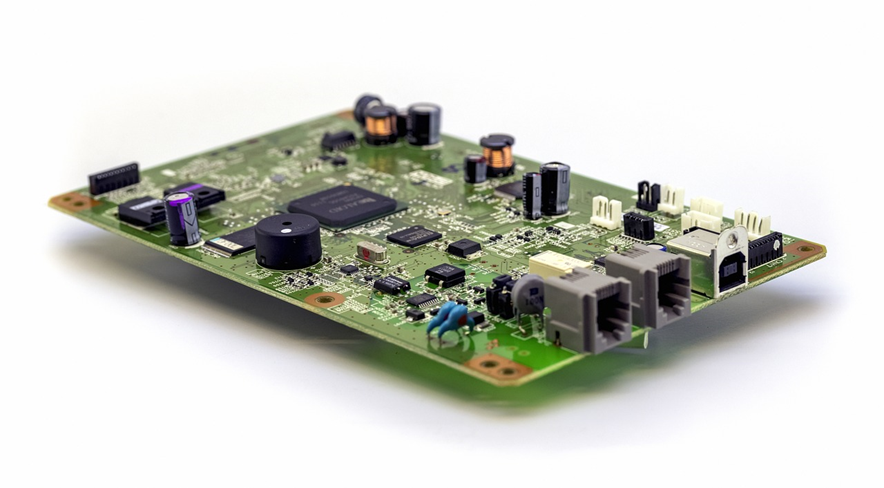
1-2 スルホール実装の手順
①部品挿入:
色々な電子部品のリードをプリント基板に開けられた穴(スルホール)に通します(実装を行います)。この実装作業は手動で行う場合もありますが、自動挿入機を使用する場合もあります。
②フラックス塗布:
はんだ付け時にはんだがきれいにできるように、フラックスを塗布します。フラックスは部品表面の酸化物を取り除く事によってはんだの流動性(のり具合)を改善する役目を果たしています。
③はんだ付け:
部品が基板に実装され必要に応じて部品は固定された後はんだ付けが行われます。この工程によってリードと基板の接触部分をはんだで埋めることで部品と基板を固定します。
④検査と修正:
はんだ付けが終了の後ははんだ付け状態などの目視検査や自動検査装置によってはんだ付け接合部分の品質チェック(確認)を行います。更に必要によっては手動にて修正を行います。
1-3 スルホール実装の用途
① パワーエレクトロニクス:
高電流や高電圧を扱う回路で、安定した接続が必要な場合に使用されます。
② 軍事・航空宇宙:
過酷な環境での信頼性が求められる機器に適しています。
③ 大型部品:
コネクタ、トランス、電解コンデンサなど、物理的に大きな部品が使用される場合にスルホール実装が選ばれます。
2.表面実装(Surface Mount Technology:SMT)
表面実装技術は電子部品をプリント基板(PCB)の表面に直接取り付ける実装方法となります。この方法(技術)はそれまでのスルホール実装に比べると基板の小型化・高密度実装・高速生産を可能にして現在の電子製品の電子部品実装に広く使用されています。
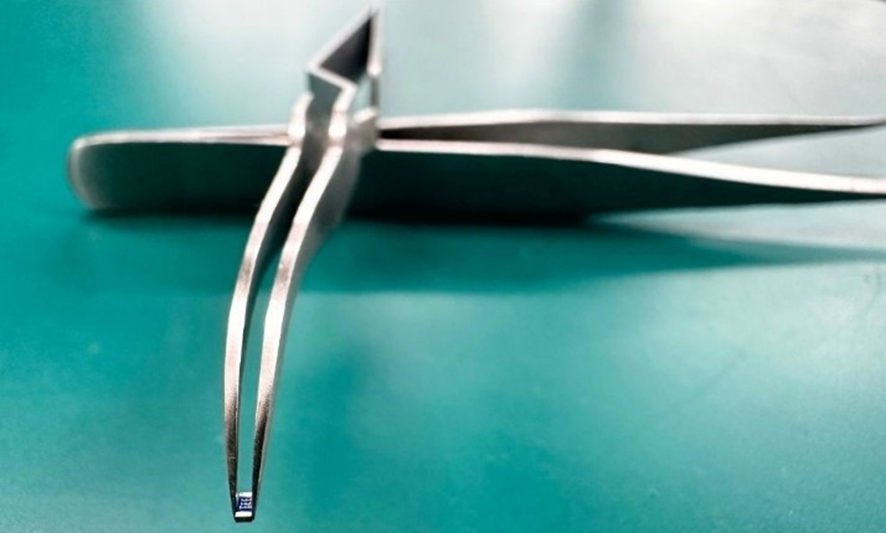
2-1 表面実装技術の特徴
①小型化・高密度実装:
部品が基板の表面に取付けられる(実装)ために基板の両面部品実装が可能となり基板面積を有効活用できるようになり、回路設計の自由度が高まり小型で複雑な回路の設計が容易にできるようになりました。
②高速生産:
表面実装(SMT)は自動化が進んでおり高速・大量生産が可能となりました。自動化された実装装置によって部品が精密に配置(実装)されるために非常に生産性が向上しています。
③多様な部品形状への対応:
表面実装(SMT)では、構造上リード(足)が無い部品・チップ抵抗・チップコンデンサーなど非常に小さな部品の使用が可能となりました。部品の形状やサイズも多種多様で柔軟な設計が可能となります。
2-2 表面実装技術の手順
①基板準備:
基板の表面には電子部品の接合部としてランド(メタルパット)が設けられています。このランドに実装する部品を取り付けるためのはんだ(ペースト状のはんだ)をスクリーン印刷やディスペンサーで塗布します。
②部品配置:
チップ部品実装機(マウンター)を使用して、電子部品を基板の適切な位置に配置(実装)します。この作業(マウンター実装)は非常に高速で精密な実装をおこないます。
③リフローはんだ付け:
部品が配置(実装)された基板は、リフロー炉と呼ばれる炉(オーブンにピザを入れるイメージをしてください)にいれます。この時温度を段階的に上昇させてはんだペーストを溶かして電子部品を基板(パット)に固定します。このことをリフローはんだ付けと呼ばれています。
④検査:
はんだ付けが完了した基板は、光学検査装置やX線検査装置などを使用して部品の実装状態やはんだ付け状態の品質を検査します。場合によっては必要に応じて修正を行います。
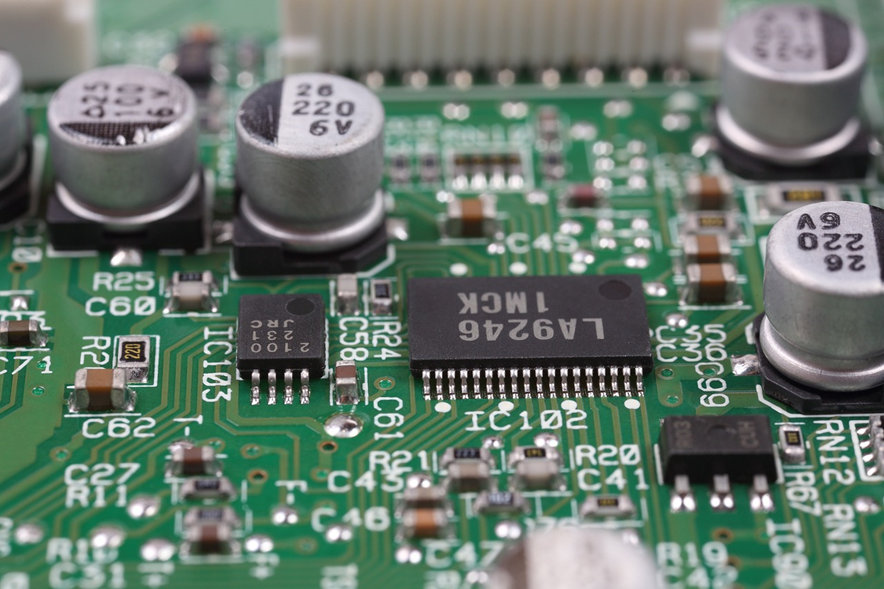
2-3 表面実装の利点
①小型化:
小型化部品を使用することができますので、製品(基板)全体の小型の実現がかのうとなります。
②高密度化:
基板の表面積を効率的に使用できますので、より多くの回路の実装が可能となります。
③生産効率:
自動化により大量生産・省力化が可能となりコストダウンになります。
3.混在実装(Mixed Technology)
混在実装はスルホール実装(THT)と表面実装(SMT)を組み合わせた実装手法のことになります。 この手法では異なった種類の部品を混在させることで一つのプリント基板(PCB)に配置しますので、設計の柔軟性や機能性が向上します。
3-1 混在実装の特徴
①柔軟な部品選択:
基板上にスルホール部品と表面実装部品を混在させることで、各々の部品の特性を最適に活用することができます。 例えば、大型の電解コンデンサやコネクタはスルホール部品で高い機械的強度を確保しながら小型のチップ抵抗やICは表面実装で高密度に配置(実装)します。
②設計の自由度:
スルホール実装と表面実装のメリットを組み合わせることで、設計技術者は機能的かつコンパクトな回路設計が可能となります。複雑な回路構成や特殊な環境条件が求められる製品には有効です。
③生産工程の最適化:
混在実装では基板製造工程において複数の工程を組み合わせる必要がありますがこれによって生産効率を最適化できます。通常は表面実装部品の配置(実装)とリフローはんだ付けの後工程にスルホール部品の挿入(実装)とはんだ付けを行う流れになります。
3-2 混在実装の手順
① 表面実装部品の配置:
基板に表面実装部品を配置(実装)します。“2-2 表面実装技術の手順”の手順に従って、はんだペーストを塗布しチップ部品実装機で部品実装を行った後にリフロー炉で部品と基板(パット)をはんだ付けします。
② スルホール部品の実装:
“1-2 スルホール実装の手順”の手順に従って表面実装部品がはんだ付けされた後にスルホール部品を挿入(実装)します。
この工程では、部品を手動で挿入することもありますが、大量生産を行う場合は自動挿入機を使用します。 その後にはんだ付けを行います。
③ 検査・修正:
最終的に基板全体の検査を実施します。必要に応じて不具合個所の修正をおこないます。この時は目視・光学検査やX線検査を行い基板全体の実装状態が正しく行われていることを確認します。
3-3 混在実装の利点
① 信頼性と高密度化:
スルホール実装の高い信頼性と、表面実装の高密度実装を組み合わせる事によって、信頼性の高い小型・高道度の基板実装製品の製造が可能となります。
② 部品の適切な配置:
大型で機械強度が必要な部品はスルホール実装で、小型・高密度な回路を構成する部品は表面実装で行って部品ごとに最適な配置(実装)方法を選択することができます。