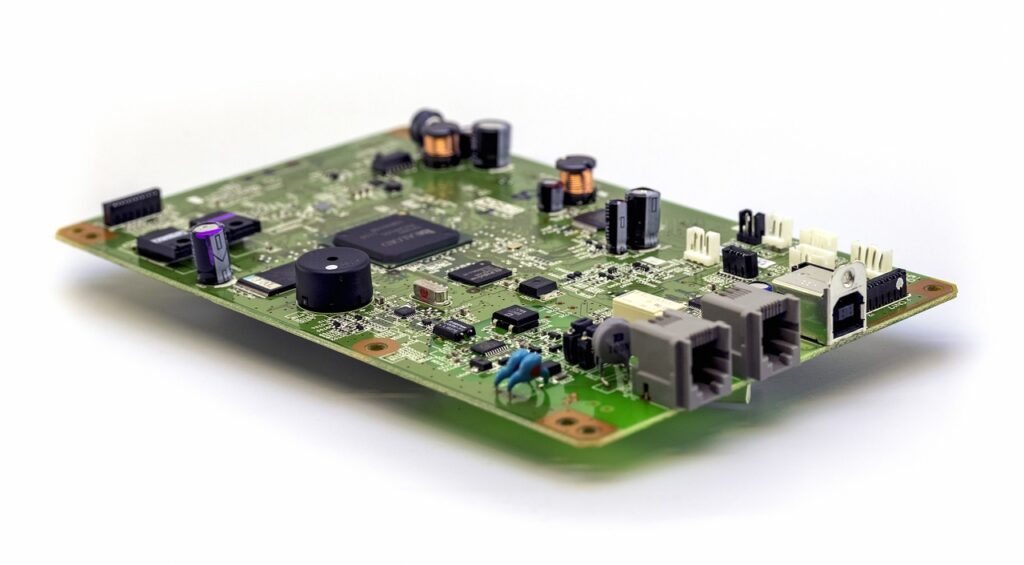
プリント基板(PCB)は、電子機器において電子部品を取り付け、配線を行うための基板です。一般的には、絶縁性のある基板材料(通常はファィバーグラス製等)に、導電性の銅箔を載せた構造を持っています。
1.概要
プリント基板(PCB)は電子機器の中で非常に重要な役割を果たしています。部品を固定するための基盤として機能し、電子部品間を配線することで信号や電力を提供しています。近年実装密度が高くなり多くの場合、複数の層(レイヤ)から構成されており、それぞれの層には導電性のパターン(トレース)があり、これらのトレースが電子部品間を電気的に接続しています。
プリント基板(PCB)は一般的には専用のCAD(Computer-Aided Design)ソフトウェアを使用してデザインしています。設計者は、部品の配置・トレースの経路・電源プレーン・接地プレーンなどを定義し、完成したデザインはファイル形式で作成されオンラインで製造工場に送られて製造されます。
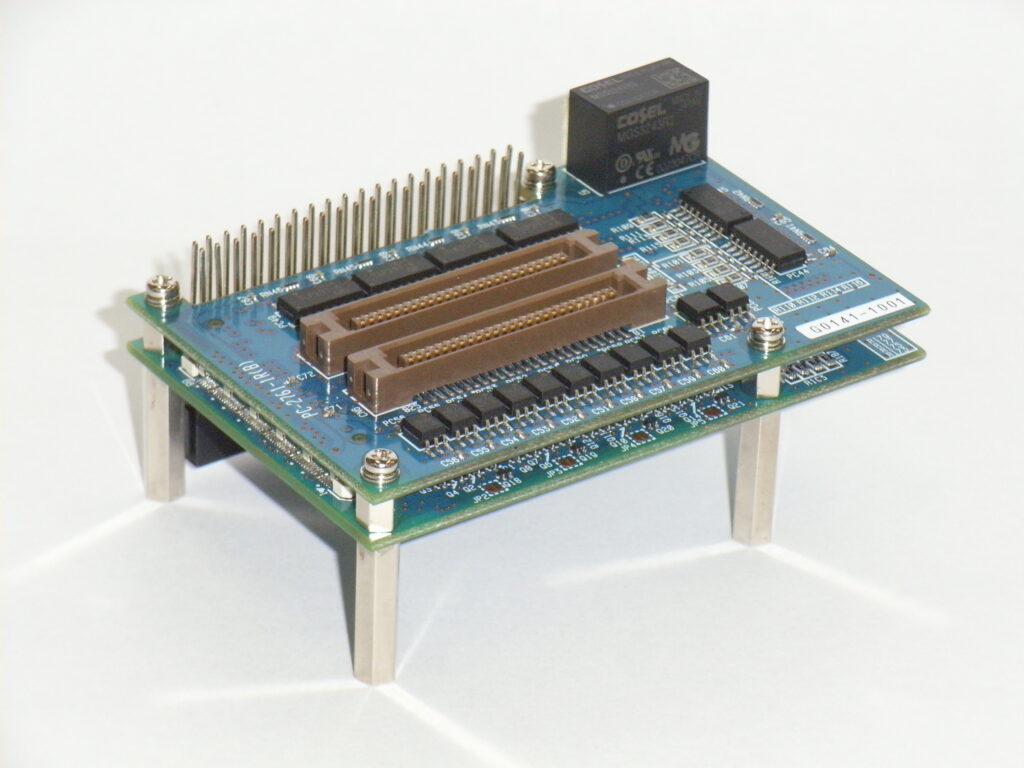
1-1 プリント基板(PCB)について主な役割について説明いたします
- 電子部品の固定と配置: プリント基板(PCB)は電子部品を固定し、正確な位置に配置するための基盤として役目をもっています。電子部品は、プリント基板(PCB)上の導電性のパッドやはんだ付け用の穴に取り付けられます。これにより、部品同士の接続と安定性を確保しています
(*)パット:チップ部品をハンダ付けする主に四角形状をしたものです。
(*)半田付け用の穴:デスクリート部品をハンダ付けする基板の表面から裏面につながっている穴(スルホール)です。
- 電気的な接続: プリント基板(PCB)上の導電性のトレース(布線)は、電子部品間の電気的な接続を提供しています。トレースは、電気信号や電力を部品間で伝送するために使用されます。複数の層からなるPCBでは、内層(内部の層)も電気的な接続に使用します
- 電気回路の形成: プリント基板(PCB)は、導電性のトレースと部品を組み合わせて、電気回路を形成します。トレースは、回路の各部分を接続し、電流の流れや信号の経路を制御します。複雑な回路を効率的に実装するための基盤として、プリント基板(PCB)は重要な役割を果たします
- 部品の保護と絶縁: プリント基板(PCB)は、電子部品を物理的に保護する役割も果たします。部品は基板上に取り付けられる為、外部からの機械的なダメージや環境からの保護を受けることができます。また、PCBの絶縁材料によって、回路の異なるセクションが電気的に絶縁され、互いが干渉しないようにしています
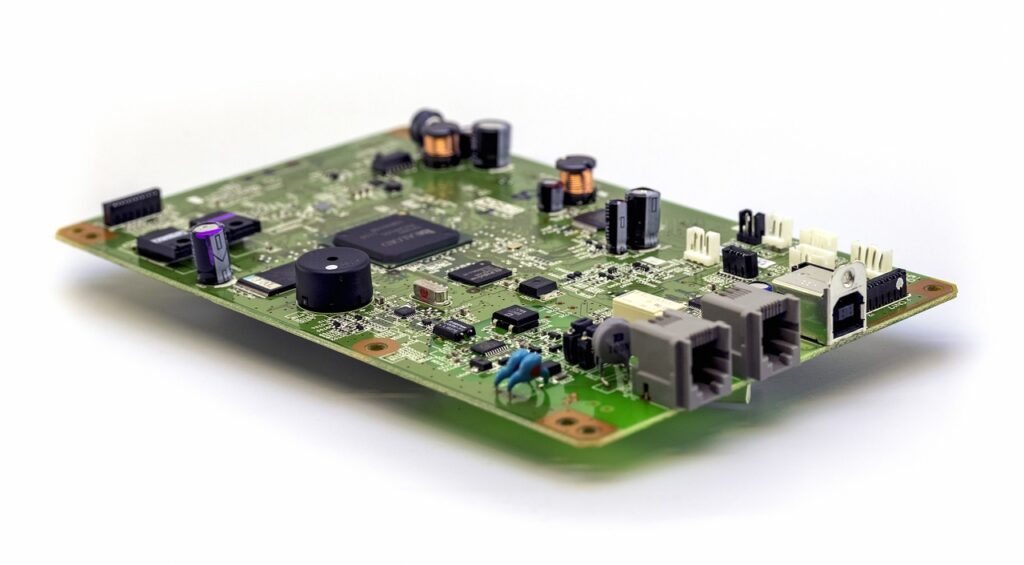
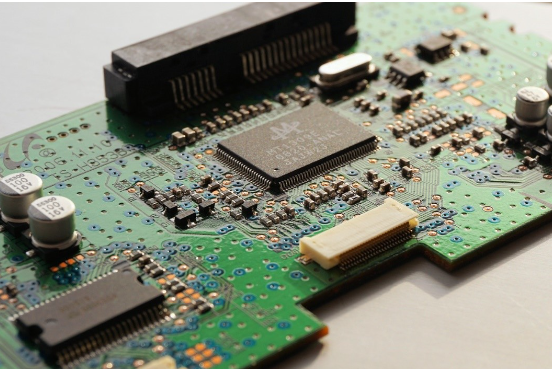
2.プリント基板(PCB)の種類について
さまざまな種類のプリント基板が存在しますが、代表的な種類について説明します。
★基板の構造の違いについて説明いたします。
2-1 片面基板(Single-sided PCB)
片面基板は、一方の側面にのみ導線と電子部品が配置されている基板です。もっとも単純な構造であり、低コストで製造されるため、一般的な電子機器や簡単な回路に使用されます。
2-2 両面基板(Double-sided PCB)
両面基板は、両側に導線と電子部品が配置されている基板です。片面基板よりも複雑な回路を設計できますが、製造コストはやや高くなります。
2-3 多層基板(Multi-layer PCB)
多層基板は、複数の層(一般的には4層以上)のプリント基板です。内部の各層には導線が存在し、層間を電気的に接続するための導通孔(ビア)があります。多層基板は高密度な回路を実現し、信号伝達や電力供給の性能を向上させることができます。高性能な電子機器や複雑な回路に使用されます。
(*)ビア:多層基板で各層間を接続する貫通の導通ようの穴(筒)のことです。
通常は一番の層から下の層まで貫通の穴(筒)ですが。各層間のみを接続するビアを使用したものをビルドアップ基板と言います。
多層基板+ビルドアップ基板を用いることで実装密度は一段と向上しています。
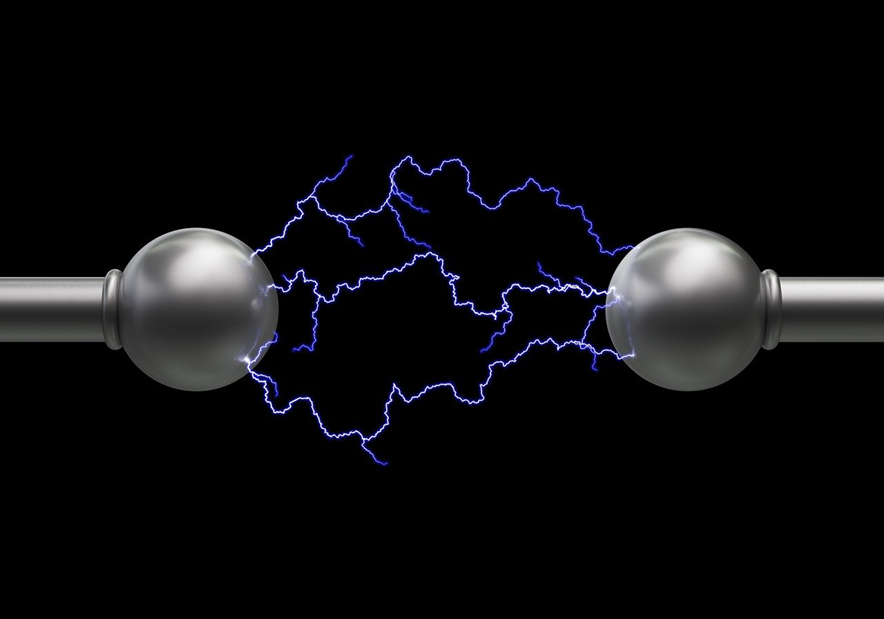
3.プリント基板(PCB)の素材について
★ここからは基板材料の違いについて説明いたします。
これらは一般的なプリント基板基材の種類ですが、特定の要件や応用によってはさらに多くのバリエーションが存在します。また、最新の技術の進展に伴い、より高密度な回路や特殊な素材を使用した基板も開発されている様です。
一般的なプリント基板(PCB)材料についていくつかを紹介いたします。
3-1 柔軟基板(Flexible PCB)
柔軟基板は、フレキシブルな素材(一般的にはポリイミドやポリエステル)で作られた曲げ可能な基板の基材です。曲げや折り畳みに耐えることができるため、制約のあるスペースや可動部分が多い電子機器に使用されます。
- 特徴:
- 柔軟性があり折り曲げることができる。
- 曲げるためには多層化は向いていない。
- 機械的強度が弱く、重い部品を実装する際には支えが必要となる。
使用用途:折り曲げる必要がある個所や可動部との接続。複数のリジッド基板を接続するハーネスケーブルの代わりに使用されることもあります。
身近のものでは、パソコンや携帯(スマホ)電話等に使用されています。
3-2 紙フェノール基板
紙フェノール基板は紙機材にフェノール樹脂を含侵した材料をしようして製造した基板の基材です。プリント基板の機材の中では歴史が古いと言われています。
- 規格:FR-1(ANSI・NEMA規格)
- 特徴:(利点)
- 価格が安い
- 切断や穴あけ加工において、ガラスエポキシ基板で必要となる特殊な工具が必要ないため、加工性が高い
- 特徴:(欠点)
- 耐久性が低いため、反りが生じやすい。
- 耐熱性が悪い。
- 吸湿性が悪い。
- 電気的特性が悪い。
- →高周波特性が悪い。絶縁抵抗が低い(高導電率である)。
- 機械的特性が悪い。
- 難燃性が低い。
- 銅メッキが不向きで、銅メッキによるスルーホールを形成できない。
使用用途:片面基板、民生機器など大量使用されコスト要求の厳しい製品に使用されます。
3-3 紙エポキシ基板
紙基材にエポキシ樹脂を含侵させた基材で製造したプリント基板の基材です。
紙フェノールとガラスエポキシ基板の中間的な特性を持っています。
- 規格:FR-3(ANSI・NEMA規格)
- 特徴:紙フェノール基板と比較すると、耐熱性、吸湿性、電気的特性に優れていますが、ガラスエポキシ基板には劣ります。
使用用途:片面基板で、絶縁抵抗性吸水性は紙フェノール基板より優れているために「高電圧回路」「耐吸水性を要求する回路」などに使用される事が多いです。
3-4 ガラスエポキシ基板
ガラス布(ガラス繊維(グラス・ファイバとも呼ばれる)を布状に編んだガラス織布)にエポキシ樹脂を含侵させた材料で製造したプリント基板の基材です。
現在一番よく使用されている基材です、両面基板を含めた多層基板のほとんどはこのガラスエポキシ基板が使用されています。基板厚みの薄い(0.2mm~0.4mm)のものから、通使われている(1.6~2.0mm)まで幅広い分野で使用されています。
- 規格:一般的耐熱性:FR-4(ANSI・NEMA規格) 高耐熱性 :FR-5(ANSI・NEMA規格)
- 特徴:(利点)
- 温度・湿度に対する寸法変化が小さい。
- 硬いため、耐久性が高い。
- 電気的特性が良い。
- 高周波特性が良い。
- 絶縁抵抗が高い(低誘電率である)。
- 機械的特性が高い。
- 難燃性が高い。
- 耐吸湿性が高い。
- 特徴:(欠点)
- 加工性が悪い。
- 専用の工具や機械を使わないと加工ができない。
- コストが高い(紙フェノール基板の2〜3倍程度と言われている)
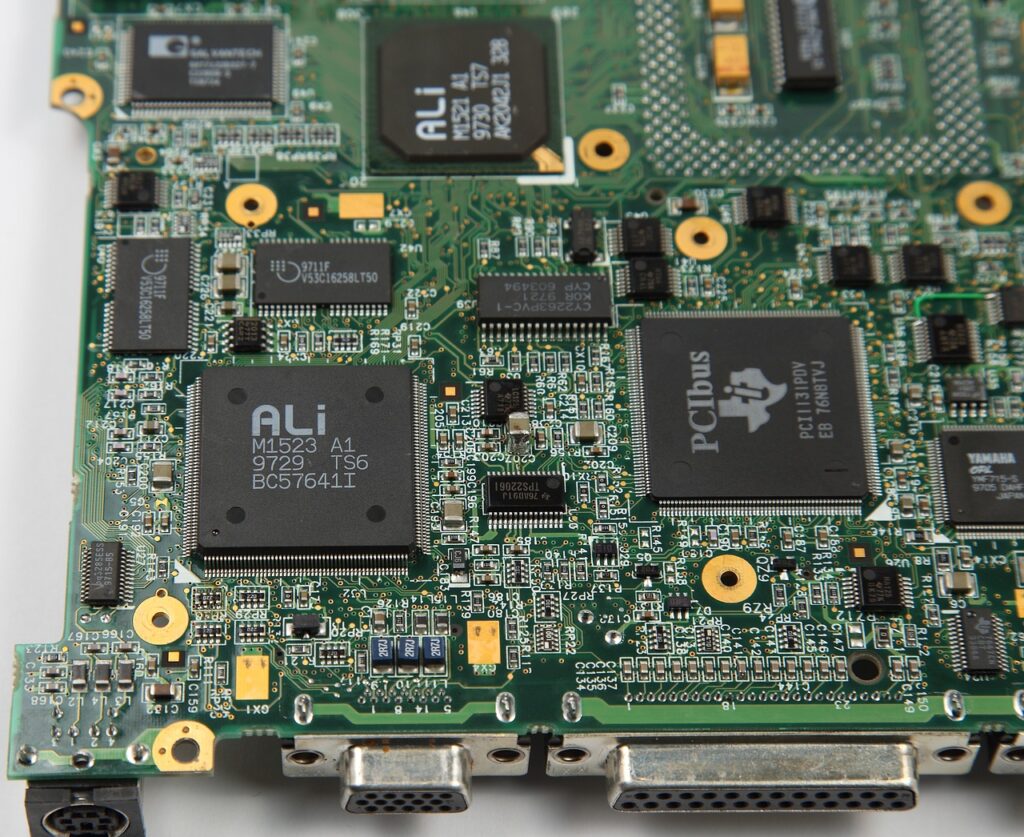
使用用途:
- 難燃性・導電率・耐久性が良いため、高信頼性や耐高周波性が求められる回路等に使われます
- 片面基板・両面基板を含めた多層基板用途とされています
3-5 金属ベース基板
アルミを材料としたプリント基板の基材です。
- 特徴(利点)
- 熱伝導性が高い
- 特徴(欠点)
- 製造コストが高くなります。
- 使用用途: 熱伝導率が高いため、電源基板・パワー部品搭載基板・大型モータの制御回路・LED搭載基板など高い放熱性が要求さられる用途で使用されています。
4.プリント基板の製造工程について
プリント基板の製造方法は、大きく分けるとサブトラクティブ法(減算法・エッチング法)と、アディティブ法(加算法)の2つに分かれます。
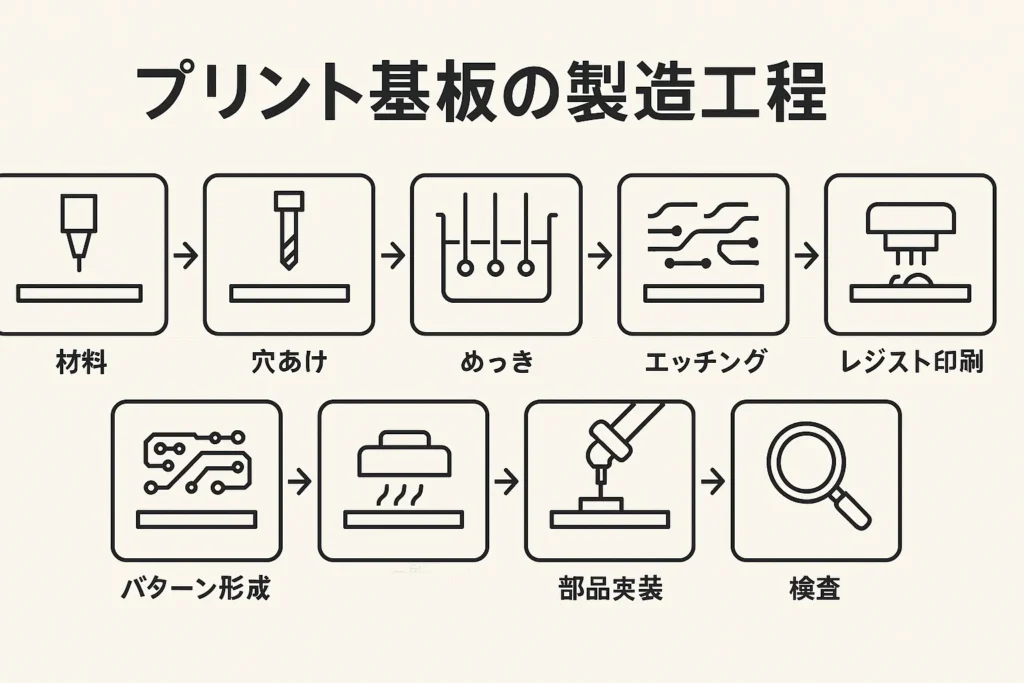
4-1 サブトラクティブ法(エッチング法)
【英語のsubtractive:減算】からきている呼び名だそうです。
サブトラクティブ法は、プリント基板の全面に貼り付けられている銅箔の不要な部分を取り除いて回路パターンを形成させる方法です。回路パターン部分をマスクで覆い、それ以外の不要な部分をエッチングによって溶かすことでプリント基板が製造されます。
引き算型の工法とも呼ばれており、製造コストの観点からプリント基板の製造工程では主流の方法となっています。
4-2 アディティブ法
【英語のadditive:加算的】からきている呼び名だそうです。
アディティブ法では、絶縁体基板に対してメッキ処理を行って回路パターンを形成していく方法です。回路パターン以外の部分にレジスト(保護膜)を形成して、レジストのない部分にメッキ処理を行うことで、回路パターンを形成します。
アディティブ法は、回路パターンを後から付け加える足し算型の工法です。
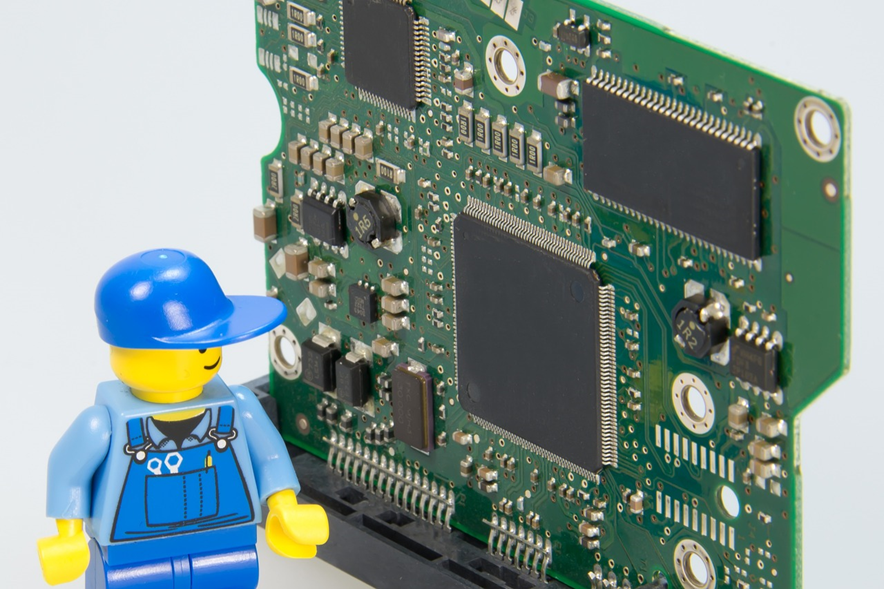
5 内層工程の製造工程
ここからは、プリント基板を製造するときの主流な工法であるサブトラクティブ法(エッチング法)での製造工程を説明致します。
プリント基板には、基板の片面に回路パターンのある片面基板。基板の両面に回路パターンのある両面基板。4枚以上の基板を重ね合わせた多層基板の3種類があります。多層基板を製造する場合は、まずは内層の製造からスタートすることになります。
5-1 材料切断
基板を加工するサイズに合わせて切断します。
この時の加工サイズとは、我々が必要とする寸法とは違う事があります。その基板メーカーで加工する上で必要な寸法となります。
5-2 フィルムラミネート
内層基板をローラーなどに通して、ドライフィルムを貼り付けます。
(*)ドライフィルム
UV(紫外線)硬貨樹脂が使われることが多いです。
5-3 露光・現像
ドライフィルムが貼り付けられた基板に回路パターンが印刷されたマスクを重ね合わせて、UV(紫外線)を照射します。UV(紫外線)があたったドライフィルムが光に反応(感光)して、基板に焼き付けられます。これを露光といいます。
回路パターンが焼き付けられた後は、不要なドライフィルムを溶解して除去します。これを現像といいます。
5-4 エッチング
露光・現像によって、基板は回路パターン以外の部分の銅箔がむき出しになった状態になります。むき出しになった銅箔を薬液によって溶かしていくのが、エッチング加工といいます。
エッチング加工後は、回路パターンに焼き付いたドライフィルムも不要になるので、除去します。
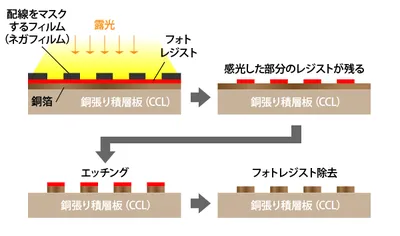
5-5 黒化処理
回路パターンが形成された内層の銅箔は表面がツルツルしており、積層したときに他の層と密着しにくくなっています。そのため、黒化処理という表面をデコボコにする処理を行って密着性を向上させます。
5-6 積層
内層の基板に回路パターンが形成されたので、基板を構成する材料を重ね合わせます。その後、積層プレス機などによって熱と圧力をかけて1枚の多層基板にします。
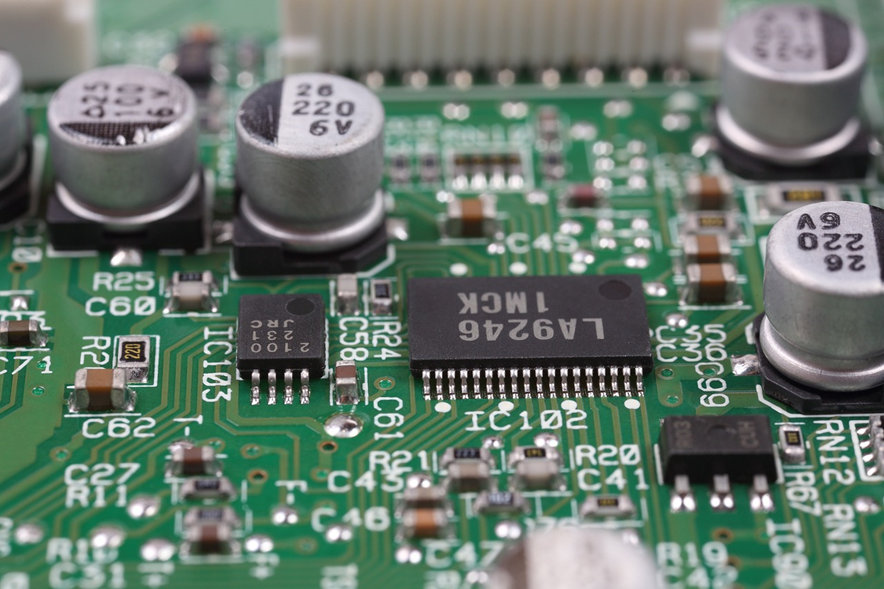
6 外層工程の製造工程
外層工程の製造工程は、片面基板、両面基板、多層基板の内層製造後に共通する製造工程です。どのような流れでプリント基板が製造されるのかを説明いたします。
6-1 材料切断
基板を加工するサイズに合わせて切断します。
6-2 穴あけ・銅メッキ
基板には必要に応じてスルーホールと呼ばれる穴をあけます。スルーホールには銅メッキを施し、電気的な接続をする役割があります。
スルーホールには、電子部品を挿入して接続するためのスルーホールと、多層基板(両面基板)において異なる層同士をつなぐためのビアホールの2つに大きく分かれます。
ドリルなどを用いて基板に穴をあけたのちに、電気的な接続ができるように銅メッキを施します。
6-3 フィルムラミネート
外層基板をローラーなどに通して、ドライフィルムを貼り付けます。
6-4 露光・現像
内層工程と同じく、外層基板にも露光・現像して、回路パターンにのみドライフィルムが焼き付けられた状態にします。
6-5 エッチング
エッチング加工によって外層基板にも回路パターンを形成したのちに、残ったドライフィルムを除去します。
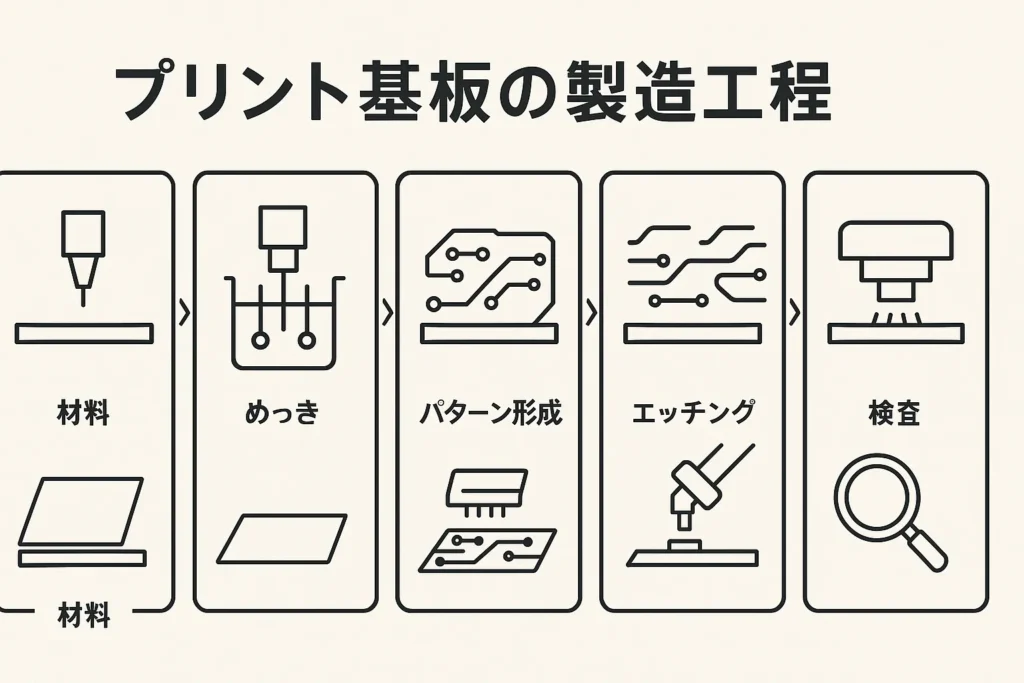
6-6 ソルダーレジスト
ソルダーレジストとは、プリント基板の表面を覆って回路パターンを保護するインクです。ソルダーレジストの主流は緑色のインクであり、私たちがイメージする緑色のプリント基板はソルダーレジスト工程後の姿となります。
ソルダーレジストは、回路パターンを保護して絶縁性を保つ、ほこり・熱・湿気などから回路パターンを守る、電子部品の実装時に不要な部分に半田が付いてショートするのを防ぐ、といった役割を持っています。
ソルダーレジストの工程はエッチング加工と近く、ソルダーレジストを塗布したのちに露光により硬化させ、不要部分を現像して除去するという流れになっています。
6-7 シルク印刷
ソルダーレジストで覆われた部分に、型名・メーカー名・電子部品の位置などの情報を書き込みます。シルク印刷と呼ばれており、インクジェットプリンタなどを用いるのが一般的な様です。
6-8 表面処理
回路パターンは銅で形成されているため、空気に触れて酸化してしまうと半田が濡れずにうまく電子部品を実装できない可能性があります。
必要に応じてめっきなどの表面処理を行うことで、銅の酸化を防いだり、半田濡れ性を高めます。半田コートや金メッキがおこなわれますが、水溶性フラックス(プリフラックス)処理も多く使用されています。
6-9 外形加工・Vカット
基板の不要な部分を外形加工で切断します。もしくは、電子部品の実装後に不要な部分を切り離しやすくするために、V字型の溝を入れるVカットを行います。
Vカットを行っておけば、容易に不要な部分を切り離すことができます。実際には専用のVカットルータの使用又は工具などを利用して、実装部品へのストレスがかからない様にしてカットを行っています。
6-10 検査
製造工程で不具合があると、断線やショートなどの問題が発生する可能性があります。品質確認のために、検査機器を用いて製造した基板の導通検査などを行います。
導通検査以外にも、キズや汚れなどの外観不良をチェックする外観検査を行う場合もあります。
- AOI(Automatic Optical Inspection)検査
基板を工学的に検査する方法です。サンプル基板と被検査品の不一致部分を検出する一方、デザインルールを逸脱した部分を抽出して良否を判定します。
- フライングチェッカー
1本のピンですべてのネットのキャパシタを検査して良否を判定する方法と、2本のピンでネットの始点と終点の導通を抵抗値から判定する2通りの方法があります。個々の基板用のデータ作成は必要ですが、次項の専用チェッカーよりは安価(初期費用)です。
- 専用チェッカー
基板のランドにピンを接触させて電流を流し、その部分の抵抗値からパターンの良否を判定します。導通状態を確認するので【オープン】【ショート】が確実に確認(チェック)することができます。 一品一様の治具であるためデータ作成の手間が少なく、費用は掛かりますが短時間(数秒)で検査が完了します。
このように、数多くの工程を経てプリント基板は製造されています。製造工法はプリント基板メーカーによって製造工程が異なる場合がありますが、ここでは一般的な流れを説明致しました。
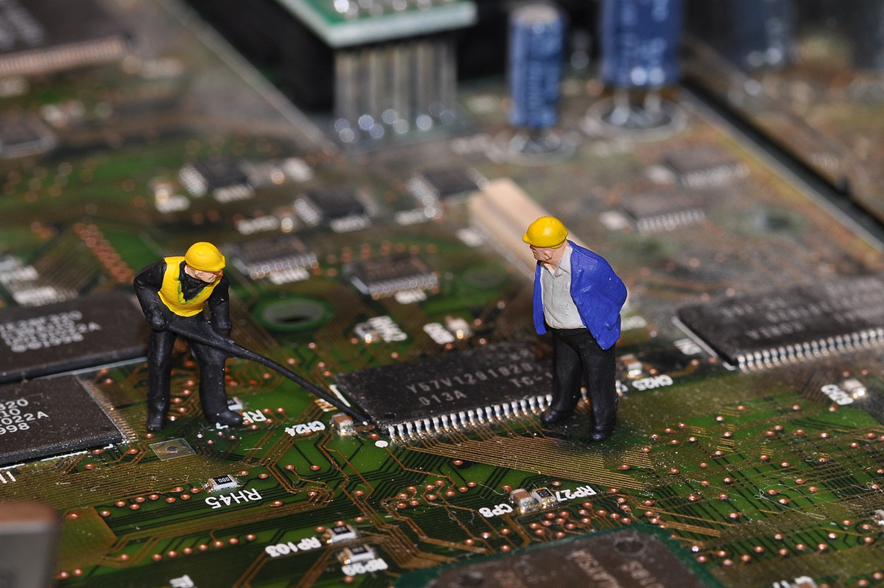